Understanding Levy-Jennings
- Bryan Knowles
- Dec 3, 2024
- 6 min read
Updated: 1 day ago
Mastering the Levy-Jennings Chart: A Crucial Tool for Laboratory Quality Control
The Levy-Jennings chart is the backbone of QC analysis in the laboratory. Let's explore it.
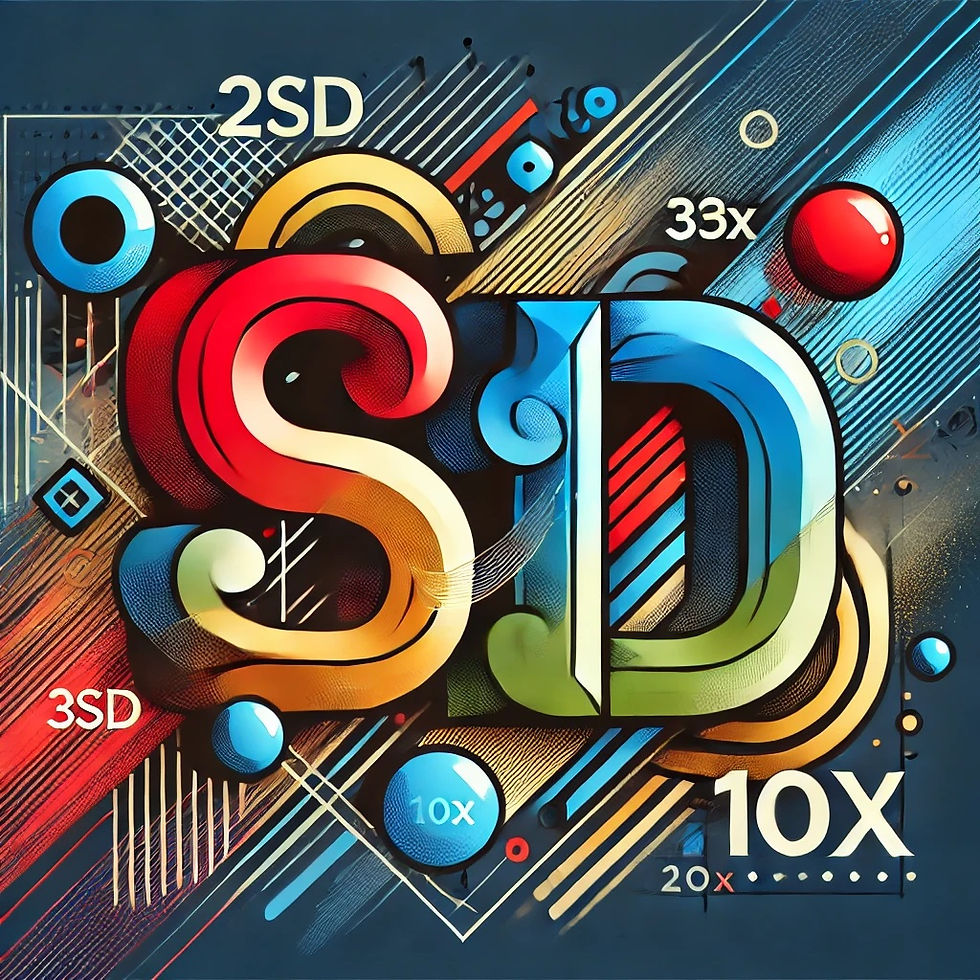
In the fast-paced and precise world of clinical laboratories, maintaining the accuracy and reliability of test results is paramount. Quality control (QC) practices are essential for ensuring that laboratory instruments and procedures produce consistent results. Among the many tools employed in QC, the Levy-Jennings chart holds a central place as a simple yet powerful graphical representation of analytical performance over time. This article explores the fundamentals, applications, and benefits of using Levy-Jennings charts, providing laboratory professionals with insights into this indispensable tool.
The purpose is really just to be able to take a quick look at your data and immediately you will see patterns or outliers.
The Levy-Jennings chart, named after S.J. Levy and J.E. Jennings, is a graphical representation of QC data over time. It is used to monitor the stability and precision of laboratory instruments by plotting QC results against predetermined control limits. Typically, the x-axis represents time or sequence of measurements, while the y-axis represents the measurement values. A central line corresponds to the mean value of the QC material, and horizontal lines denote standard deviations (±1 SD, ±2 SD, and ±3 SD) from the mean.
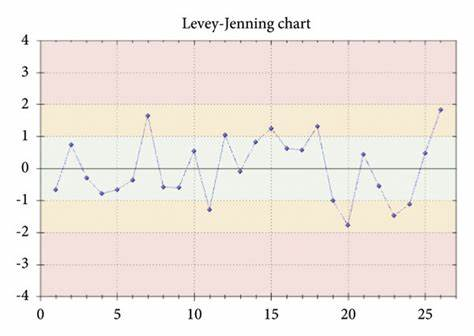
The primary purpose of a Levy-Jennings chart is to provide a visual representation of performance trends and detect systematic and random errors in a timely manner. A stable analytical process will display results that cluster around the mean, with occasional deviations that fall within acceptable limits. However, results that consistently fall outside of the control limits, or show patterns such as trends or shifts, may indicate issues such as instrument malfunction, reagent degradation, or operator errors.
Managing Levy-Jennings Rules
How do you decide which data points require a re-run of QC or whether it's a "wait and see" situation. That for you to decide. I encourage labs to get anything beyond 2SD from the mean within 2SD by re-running QC samples or other troubleshooting. This prevents runaway problems such as multiple days above 2SD. A general guideline is that you want about 19 in 20 (95%) of repetitions withing 2SD.
It is helpful to specifically set out rules and an algorithm for dealing with QC failures. Turn this into a procedure available to bench techs. A flow chart posting in the chemistry department can help greatly. See HERE for help with trouble shooting failed QC.
Westgard rules: A useful guideline
Westgard rules are a set of statistical criteria used in quality control to interpret Levy-Jennings (LJ) charts. These rules help laboratory professionals identify when a testing process is out of control, signaling potential errors that may compromise test accuracy. Here’s a summary of the key Westgard rules:
1-2s Rule: A single control measurement exceeds ±2 standard deviations (SD) from the mean. While this rule may serve as a warning, it does not immediately signal rejection. It often prompts a closer look to determine if other rules are violated. (I recommend taking action with even a 1-2S)
1-3s Rule: A single control measurement exceeds ±3 SD from the mean. This is a strong indication of a significant random error or outlier, and corrective action is typically required.
2-2s Rule: Two consecutive control measurements exceed ±2 SD on the same side of the mean. This indicates a systematic error and suggests the process is shifting away from its established accuracy.
R-4s Rule: Two consecutive control values differ by more than 4 SD (one above +2 SD and the other below −2 SD). This rule primarily detects random errors, as it highlights a large variability between results.
4-1s Rule: Four consecutive control values exceed ±1 SD on the same side of the mean. This points to a small but consistent bias or systematic error.
10x Rule (recommended): Ten consecutive control values fall on the same side of the mean, regardless of distance from the mean. This rule detects trends or shifts in the process that may indicate a systematic error over time.
7-T Rule (optional): Seven consecutive control values show a trend, either consistently increasing or decreasing. This pattern suggests gradual deterioration or bias in the analytical system.
These rules are often used in combination to ensure robust detection of errors. For example, a laboratory may require two or more rules to be violated before taking corrective action. Westgard rules are instrumental in maintaining high-quality laboratory results by promptly identifying and resolving errors, ensuring reliable test outcomes.
Interpreting a Levy-Jennings chart requires a solid understanding of control rules, such as those established by Westgard, which aid in identifying whether a process is in or out of control. For instance, a single result outside the ±3 SD line may indicate a significant random error, while trends where several points gradually move toward a control limit suggest systematic errors. Recognizing these patterns is critical for laboratory professionals to take corrective action promptly and ensure the integrity of patient results.
The benefits of Levy-Jennings charts extend beyond monitoring individual analytes. They serve as a teaching tool for new staff, illustrating the importance of QC and statistical concepts in daily laboratory operations. Furthermore, these charts support compliance with regulatory standards, as they provide documentation of ongoing quality assurance practices.
Despite their simplicity, Levy-Jennings charts are not without limitations. They assume a normal distribution of data, which may not apply to all analytes or instruments. Additionally, overreliance on the chart without understanding the root causes of deviations can lead to superficial problem-solving rather than addressing underlying issues.
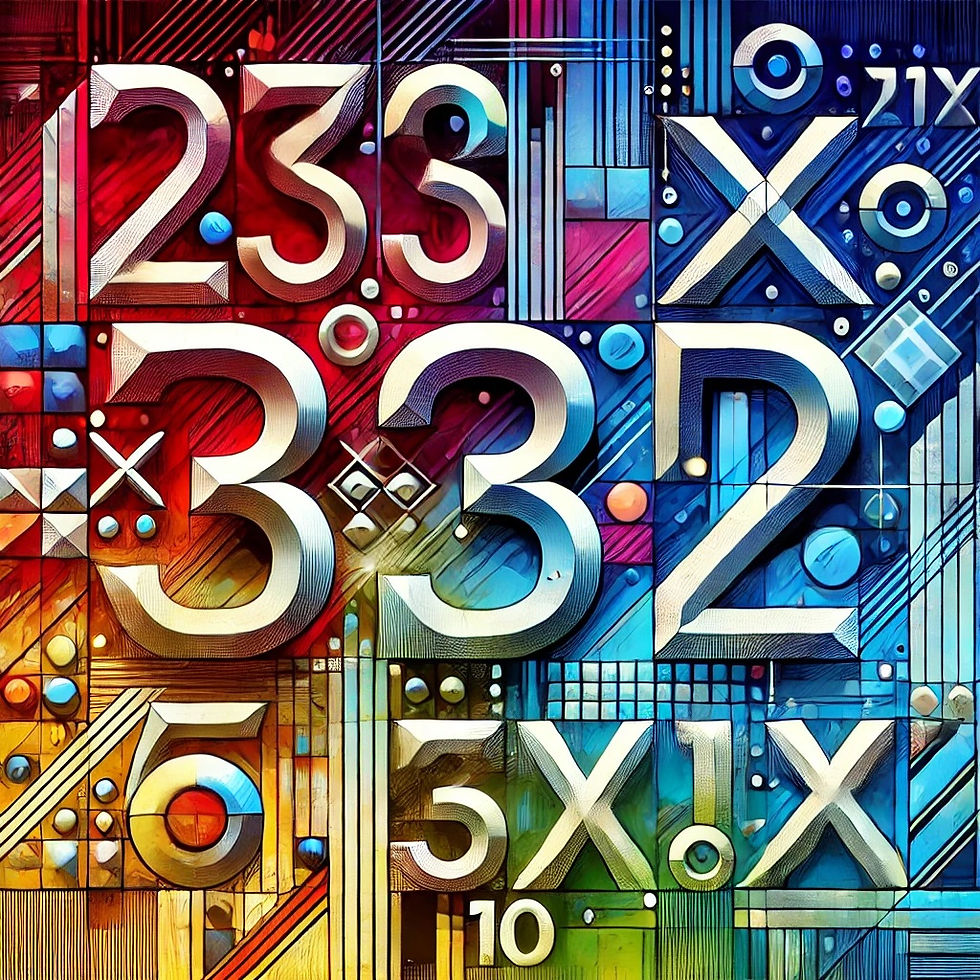
To maximize the effectiveness of Levy-Jennings charts, laboratories should ensure proper training in QC principles and provide regular evaluations of the data they generate. Pairing these charts with modern informatics tools can further enhance their utility by automating data collection, analysis, and visualization, reducing the risk of human error and freeing staff to focus on interpretation and decision-making.
If you wait until the end of the month to look at these charts, it is often too late to fix any problems that have occurred, such as missed days, troubling trends, and failed rules that weren't fixed.
Dealing With Failed QC
Initial Detection and Immediate Action
When a QC failure is detected, the very first action should be to halt the release of patient results from the affected analyzer, assay, or bench. Even if the analyzer appears to be functioning normally, continued testing during an unresolved QC failure may compromise patient safety and violate regulatory protocols. At this stage, the technologist should review the QC data to determine the nature of the failure, including which Westgard rules were violated, the magnitude of deviation, and whether it involves a single control level or multiple levels.
Documentation begins at this point. The technologist should log the failure in the QC management system or on a paper form if applicable, including time of failure, control levels involved, rule violations, and the instrument or assay in question.
Verification and Repetition of the Control
The next step involves repeating the control that failed. A single outlier may occur due to issues such as improper pipetting, control degradation, or random analyzer error. Repeat testing helps differentiate transient errors from systematic problems. If the repeated QC is within acceptable limits, the incident should still be documented, but testing may resume cautiously with close monitoring.
If the repeat control continues to fail, this points to a persistent problem that requires escalation. At this stage, patient testing must remain on hold, and the incident should be brought to the attention of the lead technologist, supervisor, or quality assurance personnel for deeper investigation.
Systematic Troubleshooting
Systematic troubleshooting must begin with the most common and easily corrected causes. This includes:
Checking reagent integrity, expiration dates, and lot numbers
Confirming proper preparation and storage of controls
Inspecting pipettes or sample probes for clogs or leaks
Rebooting the analyzer and reviewing error logs
Verifying calibration status and recalibrating if necessary
If none of these steps resolve the issue, the problem may be more complex—such as drift in optical systems, temperature instability, or deterioration of analyzer components. At this point, the manufacturer’s technical support should be contacted for assistance, and service may be required.
Each step of troubleshooting must be carefully documented in accordance with the laboratory’s quality assurance plan. The goal is to build a complete timeline of what occurred and what steps were taken to address it.
DOCUMENT, DOCUMENT, DOCUMENT!
What a helpful article! I will forward this to my team. Thanks!